Fuel Tank
I spent many hours modifying a standard tank to take the Lexus fuel pump and fuel bowl.
I was never 100% happy with it as some compromises had to be made, just because of the shape of the standard fuel tank and what I was trying to fit into it.
Non the less it was done.
I then spent even more time cleaning all the paint coating off the outside of the tank (even though it was fine and didnt need doing) so that I could get the whole thing eletro plated.
I even did the fuel tank guard too.
I then sent them off to be electroplated.
And a few days later I got it back.
Unfortunately the electro platers failed to tell me when I dropped the tank off that their process would strip every inch of zinc coating from the inside of the tank, from when Toyota had built it and deposit nothing in its place as it would be too far from the electrodes!
So I went from having a modified tank with a small amount of surface rust on the inside in places (that could have been treated with some tank sealer) to a tank with bare metal on the inside, especially between layers of metal that are impossible to seal, like where the baffle meets the main tank and is spot welded to it.
So that tank was completely f****d and there was only one place for it!
And there was only one thing for it...............
Design and build a new one from scratch.
I purchased a sheet of 3mm thick marine grade alluminium for $160 and got to work.
Cut it.
Folded it.
Clamped the 2 sections together.
Tacked them.
End section went on next.
This section needed a notch out of it for the exhaust.
I welded this seem both sides before welding it onto the tank to hopefully ensure it never leaks.
Wedged it in place with a piece of wood inside the tank.
I used a hole saw to cut a 40mm section out of some 8mm thick alluminium.
For a standard drain plug to fit into.
Drilled the center out.
And drilled another hole for it through the bottom of the tank.
In hindsight I should have drilled it 50mm further over as it ended up being right in the middle of where one of the tank straps sit.
And bolted the drain plug boss into position.
And welded it on.
Drilled some holes in the top of the tank for the standard fuel level sender, standard fuel outlets and the Lexus fuel pump.
Drilled and taped all the mounting holes for those items.
And bolted them on.
And drilled and taped the Lexus fuel pump opening.
Folded up a baffle section.
The Lexus fuel pump would bolt to this baffle.
Drilled and bolted the pump to the baffle so I could get the exact position of the baffle.
This would also dictate where the Lexus fuel bowl would be welded.
Next I welded in the Lexus fuel bowl, which has an alluminium base which gets spot welded into position.
I would have liked to have TIG'd it but didnt want to risk putting too much heat into it and melting the plastic. Also space was very tight as I had to weld looking through the hole in the top.
So I MIG'd it. Not pretty but it felt very secure.
And crucially was in the right spot.
Then I could weld the baffle in position.
Carefully and slowly so as not to put too much heat into the base of the tank as again I didnt want to melt the plastic fuel bowl.
I selected which fuel filler neck I would use and got it electro plated.
Bolted it in position.
So I could work out where the inlet on the tank needs to be for filling.
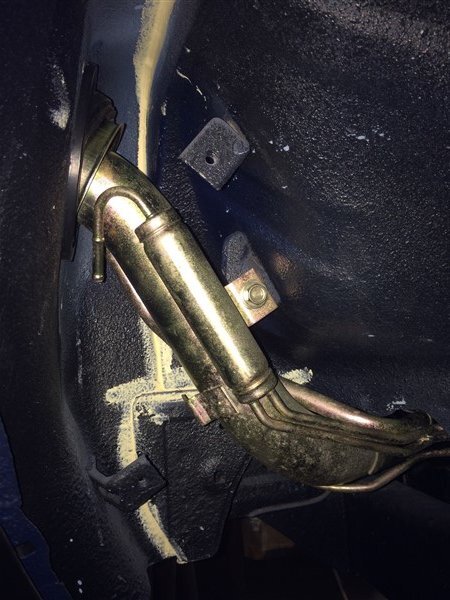